Authored by Isabel McCord
Plastic extrusion, a cornerstone of modern manufacturing, has long relied on cooling systems to maintain optimal processing temperatures and prevent overheating. Traditionally, water has been the go-to coolant. However, a growing trend towards air cooled systems is reshaping the industry. These systems are self-contained and can be supplied as turnkey ready-to-go, requiring minimum labor and installation cost, while drastically reducing downtime and maintenance upkeep compared to conventional liquid cooling. Let’s explore these cooling methods and uncover why the shift is taking place.
Why Air Cooling is a Game Changer:
Simplicity and Maintenance: Air cooling systems are remarkably straightforward to install and maintain. Say goodbye to clogged cooling tubes, the hassles of pumps, filters, coolant treatments, plumbing, and ASCO valves. With air cooling, you’ll enjoy reduced downtime and lower operational costs.
Safety First: Water and electricity don’t mix. Water leaks can lead to significant equipment damage and electrical hazards. Air cooling eliminates these concerns, ensuring a safer working environment.
Consistent Temperature Control: Air cooling often provides superior temperature control compared to water cooling, thanks to direct heat transfer between the barrel and the air. This results in improved product quality, reduced scrap rates, and enhanced process efficiency.
Energy Efficiency: While air-cooling systems require energy to operate the fans, their overall energy consumption is often lower than that of water-cooling systems, which need energy for pumping, coolant treatment, and chiller/heat exchanger operation.
Environmental Impact: Air cooling has a smaller environmental footprint. It reduces water consumption, eliminates the need for water treatment, and lowers your carbon footprint.
Cost Savings: The elimination of plumbing, ASCO valves, leaks, chillers, and heat exchangers results in significant cost savings over time.
Types of Air Cooling:
Cool-to-the-Touch Dual-Layer Shrouds: Designed with safety in mind, these shrouds feature a two-layer construction:
- Inner Layer: Constructed from solid stainless steel, this layer acts as a thermal barrier and directs airflow over the heater.
- Outer Layer: Also made from stainless steel, but perforated to allow maximum heat dissipation while remaining cool to the touch.
Multi-Versal Single-Layer Shroud: This highly adaptable single-layer shroud is ideal for both retrofit and new applications, regardless of the type of barrel band heater used.
- Solid Stainless-Steel Layer: Functions as a radiation shield, directing cooling airflow over the heater.
- Mounting Options:
- Hinge with Barrel Clamps: Designed for easy installation.
- Two Individual Halves with Barrel Clamps (Two-Piece): Perfect for installations where space is tight or mounting is challenging.
Arctic Cast Single Layer Shroud: Built for durability, this rugged shroud design is recommended for environments where the shroud system may be exposed to physical damage, such as low extruder barrel installations.
- Vented 1/4″ Thick Cast Aluminum Layer: Directs cooling airflow over the heater.
- Two-Piece Design: Consists of two individual halves bolted together and clamped around the finned cast heater.
Forced Air Blowers: These fans push air over the shroud to facilitate cooling. There are different types to suit various needs:
- Low Profile Single Phase Centrifugal Blowers: Compact and perfect for limited space.
- Standard Single-Phase Centrifugal Blowers: The most common type, offering a balance of performance and size.
- Universal Three-Phase Centrifugal Blowers: More powerful and versatile, suitable for high-output or demanding applications.
- Custom Blower Extensions: Additional components to modify blower performance, such as increasing airflow, reducing noise, or adapting to non-standard mounting locations.
Customer Insights: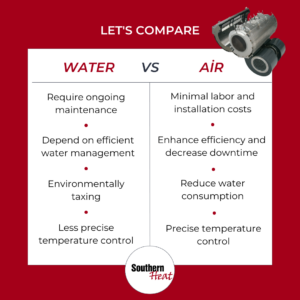
“Two years ago…I converted a Welex 4.5 and 3.5-inch co-extrusion line running ABS at approximately 2000 lbs/hr from water-cooled heating jackets to Tempco “cool to the touch” air-cooled finned heaters. I have since converted another same-size co-extruder line. We have been very well pleased with the performance of the Tempco heaters.
The benefits gained are many fold: No valves, No pumps, No tubing, No fittings, No piping, No manifolds, No heat exchanger, No deionized water, No Water Leaks, No rust, No water on the floor, No Guessing
Temperature stability greatly improved the overall process stability…the energy efficiency must be a good deal better, first after two years my two compression zones show the largest on time of 85% and 45% the other.”
Conclusion
While the initial investment in an air-cooling system may be higher, the long-term savings in maintenance, energy consumption, and reduced downtime often outweigh the upfront costs. Embracing air cooling technology is a strategic step towards a more efficient, safe, and sustainable extrusion process.
Considering the benefits of air cooling? Southern Heat can help you transition smoothly from water-based systems to an air-cooled shroud system. Our team of experts will assess your needs and recommend the most suitable air-cooling solution for your extrusion process.
Contact one of our knowledgeable sales engineers today to discuss your requirements. We’re here to answer your questions and guide you through the process.